News Story
Ghodssi wins NSF grant for microball bearing technology
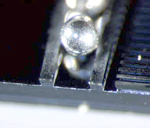
An optical micrograph of a linear microball bearing integrated in the rotor of a bottom-drive linear variable-capacitance micromotor. A stainless-steel microball with a diameter of 285 µm is sitting in a 85 µm deep, 290 µm wide silicon micromachined groove fabricated using deep reactive ion etching (DRIE). Photo courtesy Dr. Ghodssi's student, Alireza Modafe.
MEMS are not yet reliable and efficient enough for electrical and mechanical power demands in microsystems. Ball bearing mechanisms are expected to increase long-term reliability and efficiency in micro-machines through minimizing friction and wear, and to provide robustness and stability for moving parts while avoiding fabrication complexities. Therefore, "micro-ball bearing technology" is expected to have a pivotal impact on micro-machinery applications such as micro-generators, micro-pumps, and micro-coolers.
The research program investigates the use of micro-ball bearing technology for MEMS and micro-machinery applications. This goal is addressed by developing a MEMS-based electrostatically actuated micro-motor integrated with silicon micromachined bearings which house stainless-steel micro-balls as support mechanism between rotor and stator. The micro-motor is based on a novel scheme as a 6-phase, bottom-drive linear variable-capacitance micro-motor supported on micro-ball bearings. The proposed research activity focuses on (1) design, modeling, and dynamic simulation to realize an optimized structure and geometry for the device, (2) technology development to improve precision fabrication in conventional processing methods while minimizing stress-inducing processes and carefully characterizing each unit step, and (3) long-term reliability study to investigate (i) the operation of the electrical components, such as the electrical rotor and stator under controlled environment, and (ii) the dynamic behavior of the micro-ball bearings and their effect on the performance of the device.
Published September 1, 2002