News Story
UMD engineering alumni contributions aboard James Webb Space Telescope
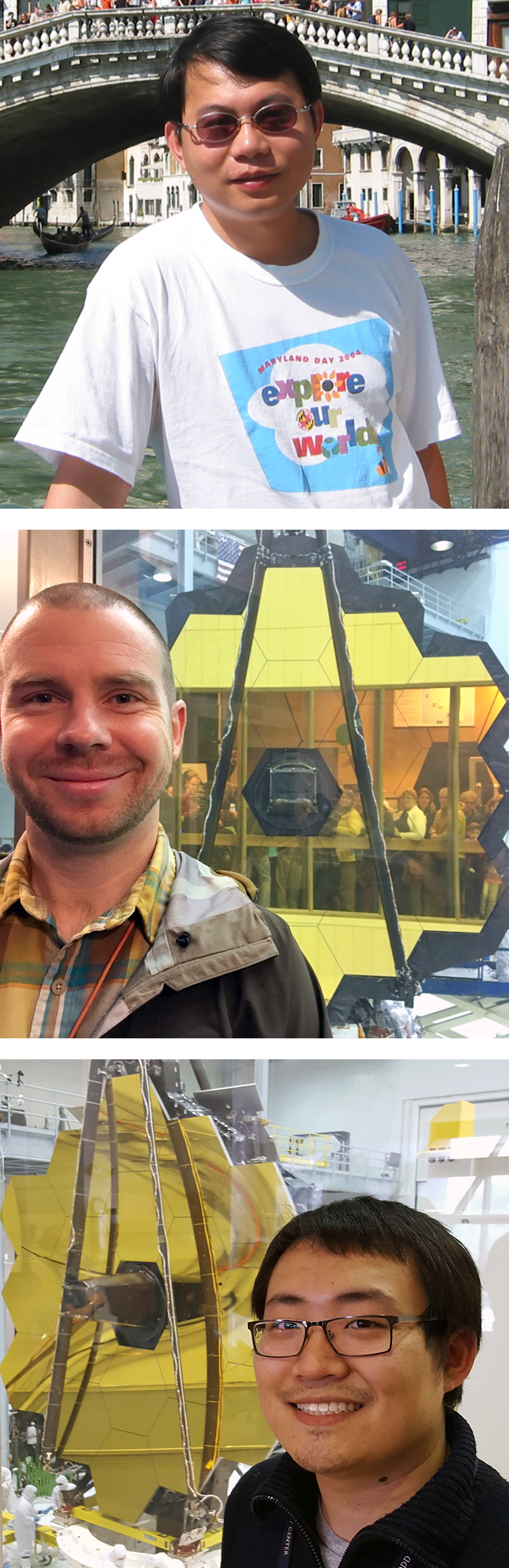
Top to bottom: Wen-Hsien Chuang, Dan Kelly, Kan Yang. Photos courtesy of the alumni pictured.
After a successful launch on Dec. 25, the James Webb Space Telescope (Webb)—the largest space observatory ever built—is well on its way to its permanent “L2” parking place 930,000 miles from Earth. The product of decades of development and testing, Webb carries contributions from a generation of University of Maryland engineering alumni.
Webb's mission is to collect infrared light from distant corners of the cosmos, enabling scientists to probe the structures and origins of the universe. Residing at L2 (the second Lagrange Point) will enable Webb to stay in a fixed position relative to the Earth and sun while expending a minimal amount of energy. It’s also the point at which the telescope’s infrared detectors can be kept cold enough (around -400˚ F) to detect the heat from the faintest and furthest objects in the universe.
Webb’s Near Infrared Spectrograph (NIRSpec), a breakthrough instrument developed at the NASA Goddard Space Flight Center, is designed to observe up to 100 space objects simultaneously. Two UMD alumni—Wen-Hsien Chuang (ECE PhD 2005) and Dan Kelly (ECE MS 2005; ECE BS 2002)—played important roles in inventing and building the micro-electromechanical systems (MEMS) microshutter array that controls how light enters NIRSpec.
Chuang helped pave the way for the microshutters by performing the first electromechanical characterization of MEMS actuators at cryogenic temperatures in his Ph.D. thesis work on MEMS-based silicon nitride thin film materials and devices. Chuang was Professor Reza Ghodssi’s (ECE/ISR) first Ph.D. student and joined Intel shortly after earning his doctorate. He has been with the company for more than 16 years.
“It’s my understanding that when we collaborated on this project with NASA Goddard, MEMS devices had not been used in outer space at cryogenic temperatures,” Chuang says. “These microshutter arrays will be the first MEMS devices operating in space.”
MEMS devices have many advantages in space applications, Chuang notes. "These include their miniature size, light weight, high resonance frequencies, short thermal time constant, and the way they can integrate with microelectronics. They can scale to very large arrays with very low mass, simple mechanical operation, and extremely reliable mechanical components for operating in the outer space environment.”
He is looking forward to seeing the implementation of his almost-20-year-old work. “As an engineer and technologist, I always like to see when my work is used in the real world and can bring benefits to the research community and human beings,” he says. “Webb will bring our understanding of the origins of galaxies, clusters, and large-scale structures in the universe to the next level!”
Dan Kelly, another of Professor Ghodssi’s early students, has spent his career at NASA Goddard Space Flight Center, where he is an electronics systems engineer in the Detector Systems Branch. Kelly’s education in MEMS microelectronics and fabrication at Maryland led to him working on the NIRSpec microshutter array for 10 years.
“From 2004 to 2014 I had the privilege of being on the team that took the microshutter array from an early concept to a space flight-qualified component,” Kelly says. “There were many challenges, accomplishments, and setbacks. The key was working with a multi-disciplinary engineering team to bring a wide array of knowledge and viewpoints, and to have fun doing it.”
He is excited for Webb to fully deploy in the coming weeks. “I can’t wait to see the first results come down from Webb during commissioning, and the incredible scientific discoveries the mission will enable,” Kelly says.
Learn more!
Webb’s 344-step full deployment should be complete by the end of January. You can see Webb’s current location in space, and how far the deployment has progressed, on this NASA page.
Read a detailed description of the NIRSpec microshutter array. View a microshutters image gallery.
Today Kelly is working on the new Nancy Grace Roman Space Telescope, scheduled for launch near the end of this decade. He is the Product Design Lead for its Sensor Control Electronics subsystem. The Roman telescope will probe the expansion history of the universe, the effects of dark energy, the consistency of general relativity and the curvature of space-time.
A UMD alum also played a key role in determining whether Webb’s instruments would work in the extreme cold of space.
NIRSpec and the other instruments aboard Webb were designed to perform in a thermal environment with temperatures near absolute zero so they would be able to detect the infrared heat produced by distant stars. It was important to test whether the components could withstand the cold and operate as expected.
“If there were any issues, we wanted to be able to understand and fix them here on the ground,” alum Kan Yang (AE MS 2010) says, “since, unlike the Hubble Space Telescope, Webb will be too far away to be serviceable.”
As the Lead Thermal Analyst for the OTIS Cryo-Vacuum Test, Yang was responsible for developing a way to cool the telescope to the temperatures that it would be exposed to in space; to establish the thermal conditions to perform the optical, thermal, and thermal distortion tests; and then to warm everything back up to room temperature.
“This operation is much more complex than just placing the telescope in a cold refrigerator,” Yang says. “Many sensitive components on the telescope cannot tolerate large thermal gradients or rapid swings in temperature, and needed their temperatures to be controlled precisely upon cool-down or warm-up. Otherwise they would be stressed beyond their intended design limits and break.”
Years of thermal analysis and hardware preparations were needed to find the safest and most efficient method. In the end, NASA used the world’s largest thermal vacuum chamber at the Johnson Space Center in Houston in a test lasting 90 days from start to finish.
“Ultimately, my work helped us confirm that Webb will achieve the temperatures that we’re intending for it to cool to after launch,” Yang says. “We were able to ensure it will work at those temperatures so it can execute the full breadth and scope of its science mission.”
Yang currently helps lead a team of engineers performing rapid, concurrent and collaborative design studies for many different types of spaceflight instruments in NASA Goddard’s Instrument Design Lab. At UMD, he was advised by Professor James Baeder (AE). While his graduate education focused on helicopters, “Maryland certainly equipped me with the correct tools and mindset on how to approach complex engineering problems,” he says. “Aircraft and spacecraft are all designed and analyzed using the same physics principles and require the same engineering processes and teamwork. UMD did a great job in imparting those lessons.”
Yang worked on Webb from 2013 to 2019. “Six years may seem like a long time,” he says, “but I was a relative newbie versus a lot of the senior members who established their entire careers on this telescope. Webb was by far the longest and most complex project I have worked on in my NASA career. It’s an incredible experience to be surrounded by so many brilliant people tackling engineering challenges and working towards a scientific instrument that will revolutionize our understanding of the universe."
Published January 2, 2022